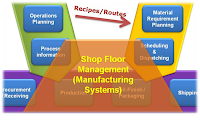
Analytics header
Monday, September 27, 2010
Common question - What MES should I use?
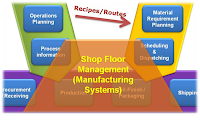
Friday, September 17, 2010
Extreme Gobbledygook - Funny
Thursday, September 16, 2010
Next week at CBI MES conference
Next week I will be at the CBI MES conference in
I also look forward to the conference because I have never been to
Friday, September 10, 2010
"Lean technology" a Manufacturing Systems perspective
- Value stream: We all know that value is identified by the specific needs of the customer hence the Manufacturing System should be usable and implementable to support only these specific processes that add value. In other words the system once implemented should not require or be constrained to use extra processes or involves extra steps if they are not directly part of the value flow.
- Implement flow: The Manufacturing System should employ a value centric process model that is easily managed and accessible to all the relevant people. This will allow a transparent view of the value flow and thus allow engineers and operators to ensure production flow, be it a one-piece flow, supermarkets, or other relevant Lean solutions.
- Execute Pull: This is kind of the obvious requirement that involves the enablement of pull execution and dispatching of WIP. This may include features and functionality to enable or enforce flow and managing kanbans, supermarkets, balancing, etc.
- Enable Perfection: Enable perfection by providing the production and process visibility needed for the continuous improvement efforts. This is the part of the system that provides Intelligence (a topic that I have written a few relevant posts about). In addition the Manufacturing System should provide adequate configurability, extendibility and customizability that support continuous improvement.
Wednesday, September 1, 2010
What is it that I do?
I help people and companies in the pharmaceutical and biotechnology industry that produce medicine, drugs and tools for doctors with their computer systems. The use computers to make sure that their products have no defects, as wells as to make sure that they produce their products exactly the way the recipes instruct. The computer systems save and maintain all the information during the production so that it can be used to analyze what happened if there is a defect, or how to improve the production process. The computers also help automate some of the steps in the process.